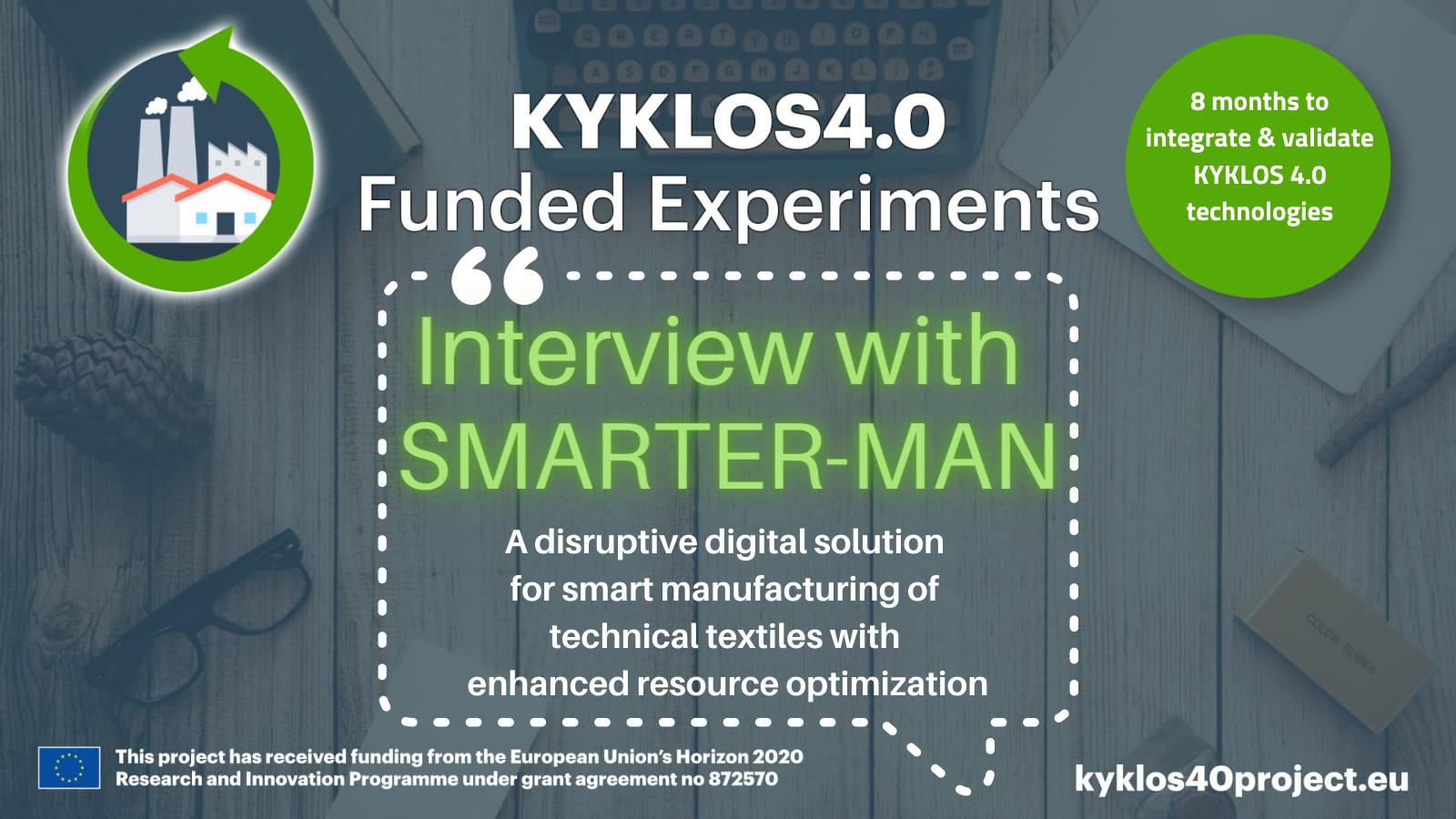
01 Aug Interview with the SMARTER-MAN experiment
The KYKLOS4.0 Open Call #2 is funding seventeen experiments that are developing technological solutions of value for the manufacturing domain.
The project will be releasing a series of interviews over the course of the coming weeks with the objective of promoting the work being implemented in these experiments and allowing our readers to understand potential uptake of the solutions being developed by them.
This is the sixteenth of the seventeen interviews with the experiments funded under the open call. Today, we interview the SMARTER-MAN experiment.
* * * * *
Explain your project in one sentence.
In order to digitise and automate its manufacturing processes, LIASA is partnering with the technology provider APM, a company with vast expertise in developing and integrating game-changing industrial 4.0 solutions such as IoT sensors, a Work Order Management Software and ERP systems to monitor the production of its assets. The proposed solution, SMARTER-MAN, consists of a disruptive digital industry 4.0 solution for smarter manufacturing of elastic cords and will bring major benefits to LIASA and its potential customers. Such array of benefits include: reduced lead times and machine downtime with improved asset utilisation, less waste generated and lower manufacturing labour costs, and ultimately an optimised product quality leading to enhanced price-performance ratio of the new added value products to sell to the targeted customers, with greater delivery reliability.
How is KYKLOS4.0 project and the selected services (and components) bringing value to your project?
The advanced production control software will be able to provide a wide array of benefits: as it will be possible to automatically calculate the optimal sequence of production orders online and in real-time, towards a flexible industrial production capable of anticipating disruptions on both the supply and demand side. The deployment of the new production planning module (WOM) should support LIASA in (i) Automatic calculation of resource utilisation: process duration at each process line/workstation, operator/work assignment, history of all the modifications made in an order cycle (who, when and why), forecasting how alterations in the production parameters and machine stops will impact delivery times and accuracy of the orders (enabling preventive maintenance). (ii) calculate the exact units manufactured from a production order in a machine at any given time, (iii) Obtain the real net production capacity of a machine for a given item (in real-time), and with greater accuracy estimate the production capacity of a never-before-made item. (iv) enforce circular economy target: 5% improvement in recyclability/reuse, managed by reducing the waste generated through increased process parameters control (real-time monitoring of tensile strength of the tapes will ensure higher quality products, thus less non-conformities and waste)
How is your solution contributing to circular manufacturing?
By implementing novel digital technologies we are supporting the optimisation of the textile production processes. The types of operational efficiencies that a smart factory can provide may result in a smaller environmental footprint than a conventional manufacturing process, with greater environmental sustainability due to maximised asset utilisation and predictive maintenance. Reusability/Recyclability/Recoverability (RRR) rate (circular KPI selected) estimates the fraction of the product that is potentially reusable/recyclable/recoverable at the end of life. Target: 5% improvement in recyclability/reuse, managed by reducing the waste generated through increased process parameters control (real-time monitoring of mechanical tension of the fabrics will ensure higher quality products, thus less non-conformities and waste). By reducing resource use and prolonging the useful life of textiles, this model enables the loop to be closed by turning waste textiles into raw material for new textiles or other production chains.
How will your solution be replicated and used in other manufacturing environments?
The current maturity of our digital industry system (IoT sensors, WOM, and ERP software) has been developed into a complete system by the technological partner (APM) reaching a TRL7 (“system prototype demonstrated in operational environment”). Those prototypes are highly tailored to the textile sector, and to LIASA manufacturing operations in particular, since both companies have been collaborating over the past few years. However, a complete system like the one envisioned in this proposal is not fully implemented yet and the goal for LIASA is to get the actual system proven in an operational environment within the project runtime reaching TRL8.
What advice would you give to companies wishing to make their manufacturing processes more circular?
The European Commission has launched its industrial strategy in 2020 (updated in May 2021 to take into account the new circumstances following the COVID-19 crisis) including a list of actions to support the green and digital transition of EU industry3. We will be supporting the business case for green and digital transitions through the increase of the efficiency of the manufacturing processes in the textile sector. The COVID-19 pandemic has brought a negative economic impact into the textile sector: EU turnover (€85 billion) for textiles decreased by 9.3%. This project will represent a clear opportunity to strengthen the resilience of the sector in the single market, leveraged by an EU partnership.
Our implementation of digital technologies will also play a critical role in the achievement of the United Nation’s Strategic Development Goals (SDGs):
-SDG No. 9: “Industry, Innovation and Infrastructure” – by investing in new technologies (e.g. Investing in IoT, Data Analytics and Management, and Decision making support tools) to enable industry growth through new and more sustainable innovative solutions;
-SDG No. 12: “Sustainable consumption and production” – by implementing novel digital technologies we are supporting the optimisation of the textile production processes. The types of operational efficiencies that a smart factory can provide may result in a smaller environmental footprint than a conventional manufacturing process, with greater environmental sustainability due to maximised asset utilisation and predictive maintenance. Reusability/Recyclability/Recoverability (RRR) rate (circular KPI selected) estimates the fraction of the product that is potentially reusable/recyclable/recoverable at the end of life. Target: 5% improvement in recyclability/reuse, managed by reducing the waste generated through increased process parameters control (real-time monitoring of mechanical tension of the fabrics will ensure higher quality products, thus less non-conformities and waste). By reducing resource use and prolonging the useful life of textiles, this model enables the loop to be closed by turning waste textiles into raw material for new textiles or other production chains.
Improving productivity, efficiency and sustainability is the way to transform the European textile industry, laying the foundation to shift current manufacturing trends and encourage higher margins for companies and better conditions for workers, potentially boosting industry performance compared to overseas.
Our strategy is clearly aligned with the EU industrial policy that would support the twin green and digital transitions, aiming to make EU industry more competitive globally, and enhance Europe’s open strategic autonomy. ICT-based solutions applied across the manufacturing value chain help to make processes more efficient. We will enable the creation of more sustainable, personalised, diversified and mass-produced products as well as flexible reaction to market changes (fulfilling the new Industry 5.0 paradigm).
* * * * *
About the SMARTER-MAN project
The SMARTER-MAN project –A disruptive digital solution for SMARTER MANufacturing of technical textiles with enhanced resource optimization – is implemented by two partners: APM Comercial Informàtica S.A. (Spain), LA INDUSTRIAL ALGODONERA, S.A. (Spain)
Summary: The main objective of the project is to develop a digital Industry 4.0 solution for smarter production of elastic cords, to reduce machine downtime and waste generation, lower labour costs and improve product quality, resulting in higher customer satisfaction and increased profits.