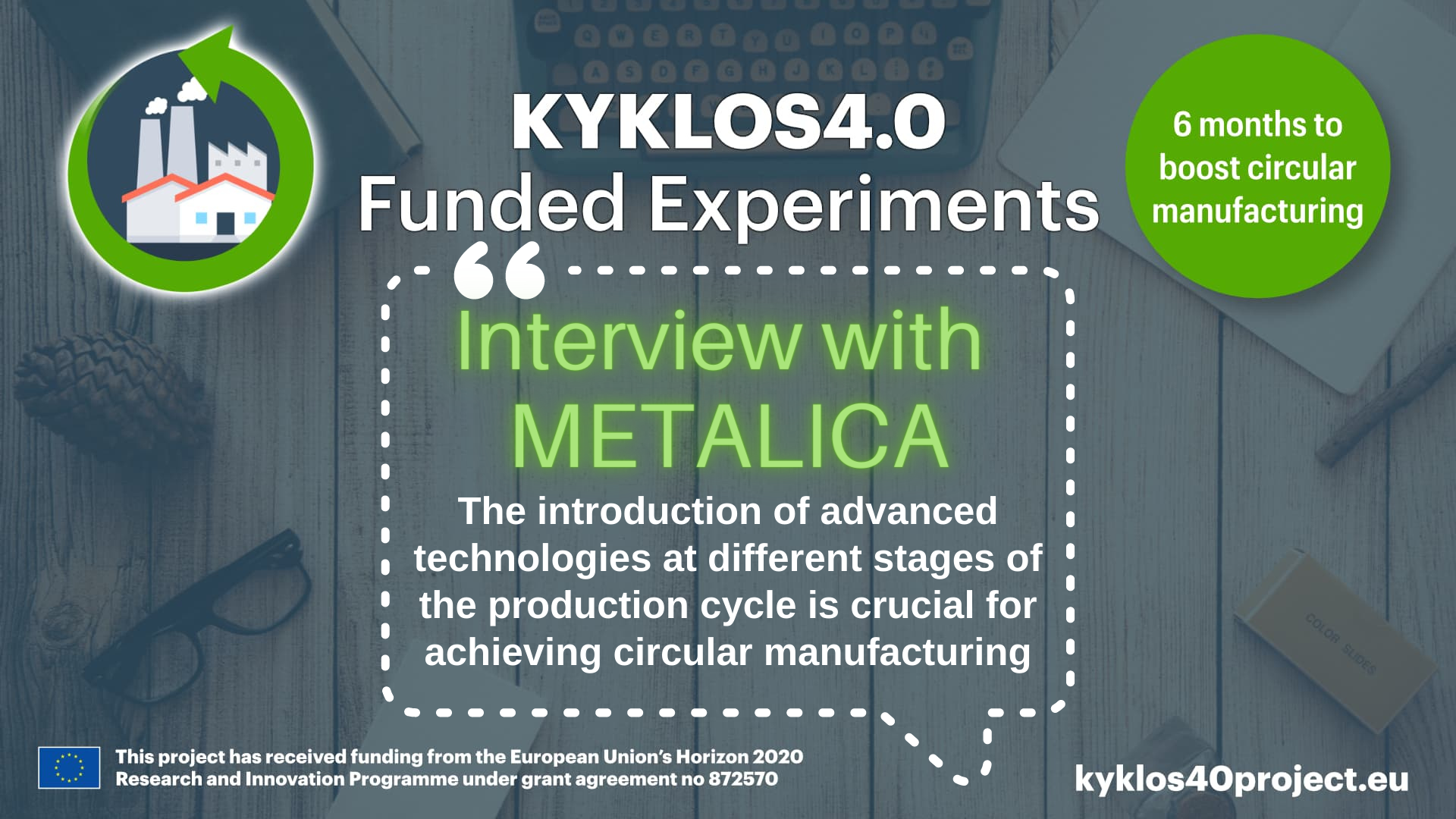
02 May Interview with the METALICA experiment
The KYKLOS4.0 Open Call #1 is funding seven experiments that are developing technological solutions of value for the manufacturing domain.
The project is releasing a series of interviews over the course of the coming weeks with the objective of promoting the work being implemented in these experiments and allowing our readers to understand potential uptake of the solutions being developed by them.
This is the sixth of seven interviews with the experiments funded under the open call. Today, we interview the METALICA experiment.
* * * * *
Explain your project in one sentence.
The METALICA project implements a novel and configurable digital tool for lifecycle assessment (LCA) and condition-based maintenance (CBM) of smart pipes, by leveraging advanced technologies such as Digital Twin, Machine Learning and Augmented Reality.
How is KYKLOS4.0 delivering value to your project?
The METALICA project benefits from getting access to the KYKLOS 4.0 ecosystem and utilising the assets that it offers. Advanced technologies provided by KYKLOS 4.0 are exploited to develop an innovative METALICA digital tool. Specifically, high quality KYKLOS 4.0 components and modules are accessed and evaluated, while the most suitable are adjusted and integrated into the METALICA solution with support from the KYKLOS 4.0 consortium. Moreover, the METALICA team closely collaborates with the KYKLOS4.0 partners, exchanging ideas and knowledge about pioneering technology approaches.
How is your solution contributing to circular manufacturing?
The METALICA solution creates a new manufacturing model, optimising the use and quality of constructed pipes, while eliminating waste associated with defects. The system is utilised during the production of smart pipes, as an intelligent testing and defect inspection toolbox. Innovative technologies are exploited to identify the exact location of defect on a pipe, leading to Zero Defect Manufacturing. Specifically, METALICA creates a configurable Digital Twin that identifies discrepancies in the production of smart pipes in near-real time by leveraging Machine Learning techniques to analyse the produced LCA and CBM. The pipe’s defect is visualised by Augmented Reality, and can consequently be repaired. The developed solution has a strong “green nature”, as it is aimed at reducing water loss and environmental impact associated with the repair and replacement of pipes.
How will your solution be replicated and used in other manufacturing environments?
METALICA creates a configurable and modular digital twin to optimise the manufacturing of smart pipes, by modelling the pipes as Cyber Physical System (CPS), deploying sensors, as well as acquiring and analysing data. The fact that the digital twin is modular and configurable in terms of data sources (e.g., sensors), data collection rates and analytics modules/algorithms, makes it a valuable asset that can be easily adjusted and used in different manufacturing industries. The digital twin can be extended with smart functionalities regarding LCA and CBM as well as what-if analysis of various factors that better suit each manufacturing process.
What advice would you give to companies wishing to make their manufacturing processes more circular?
In recent years, an increasing number of manufacturing companies have had the will to make their manufacturing processes more circular. The introduction of innovative and advanced technologies at different stages of the production cycle is crucial for companies that want to achieve this aim. Those technologies should simplify the different processes, assess the environmental impact, and assist in the minimisation of the produced waste. For instance, data can be acquired by sensors during the manufacturing processes and analysed to make the right decisions about LCA. The above result in the creation of goods that can be used for longer, while the environmental impact is considered during their production.
* * * * *
About the METALICA project
The METALICA project – Smart Pipes’ Manufacturing Inspection, Testing and Life Cycle Analysis – is implemented by two partners: Synelixis Solutions S.A. (Greece), the coordinator, and EKSO S.r.l. (Italy).
Summary: The main objective of the project is to implements a novel, modular, configurable, and intelligent solution for lifecycle assessment and condition-based maintenance of pipes used in hydraulic networks.