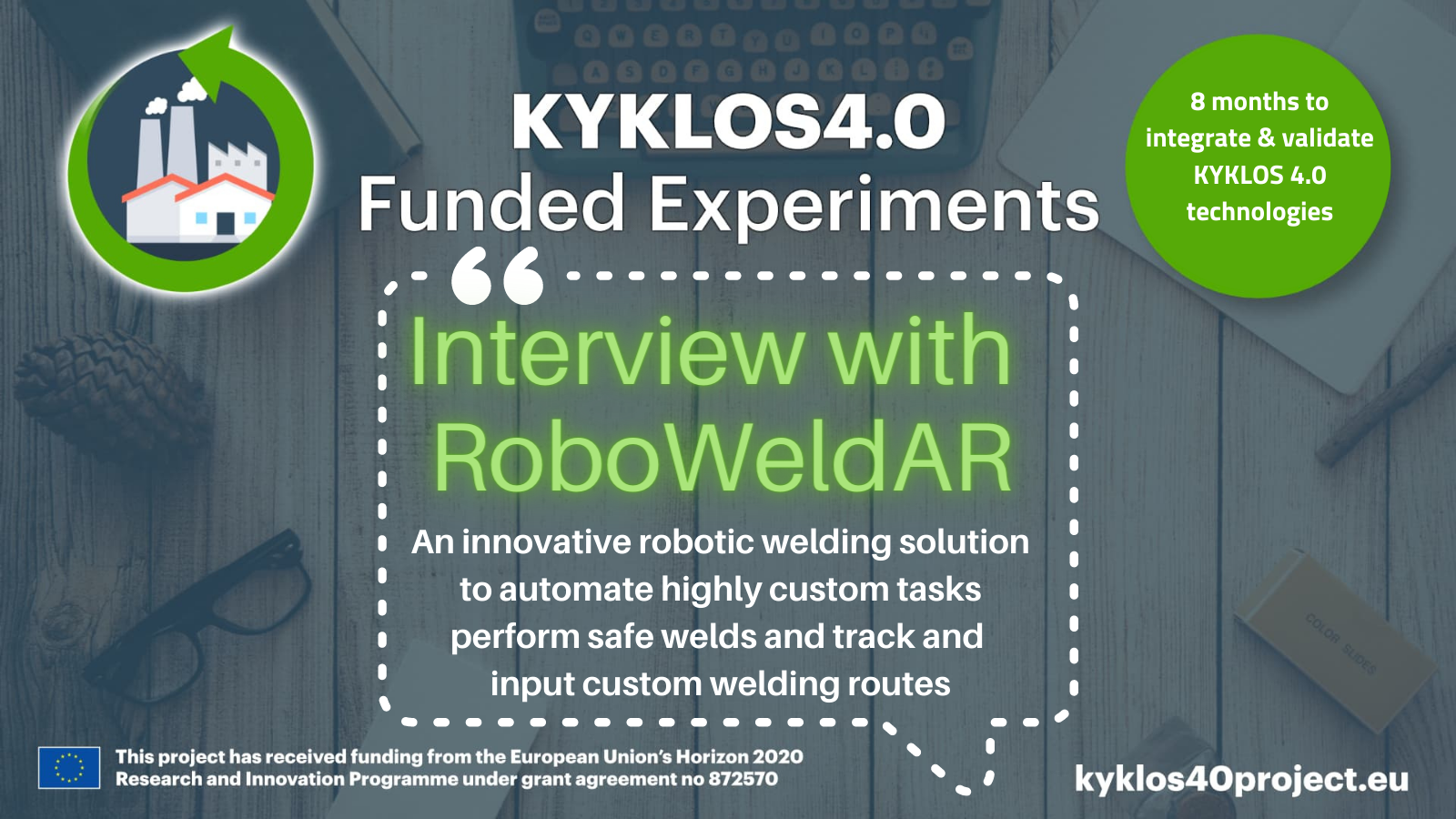
26 Jul Interview with the RoboWeldAR experiment
The KYKLOS4.0 Open Call #2 is funding seventeen experiments that are developing technological solutions of value for the manufacturing domain.
The project will be releasing a series of interviews over the course of the coming weeks with the objective of promoting the work being implemented in these experiments and allowing our readers to understand potential uptake of the solutions being developed by them.
This is the fourteenth of the seventeen interviews with the experiments funded under the open call. Today, we interview the RoboWeldAR experiment.
* * * * *
Explain your project in one sentence.
RoboWeldAR is an innovative, self-navigating robotic welding solution that will revolutionise the ship newbuilding and repair industry by automating highly custom tasks in agnostic environments and by performing high quality and safe welding tasks, while providing technicians with the ability to monitor and easily insert custom welding trajectories.
How is KYKLOS4.0 project and the selected services (and components) bringing value to your project?
IKH will develop an Augmented Reality (AR) application for the HoloLens 2 headset using the KYKLOS 4.0 AR component to enable robot-operator interactions. The available components (Front end, AR based content editor and AR based reconfigurator tool) will help design the app, visualise it and display sensor information to the operator of RoboWeldAR. The app is projected to consist of virtual control panels that will give the operator a comprehensive set of controls to easily coordinate the robot’s actions, provide vital status information, operation instructions and useful digital twin visualisations. Unique to AR is the capability of mixing the real with the digital world, giving the operator an easy way to validate the robot’s understanding that its workspace matches the physical reality and thus prevent mistakes from happening. The augmented reality experience wishes to put the human in the loop in a meaningful way, in charge of the high-level workflow but away from toxic fumes and repetitive, labor-intensive tasks.
How is your solution contributing to circular manufacturing?
RoboWeldAR uses a machine learning DSS (Decision Support System), trained with real-world data, to determine the optimal welding parameters (amperage, feed rate, travel speed, etc.) for each selected task based, in part, on information gathered from its sensors. Thanks to this advanced decision support system, RoboWeldAR performs a high-quality weld from the first try, leading to a reduction of defective welding material, wasted electric power, welding wire, shield gas and CO2 emissions. Hence, RoboWeldAR achieves the circular economy objectives of reducing inputs and the use of natural resources, reducing valuable materials and energy losses and reducing emissions levels. Moreover, a significant result of a higher-than-average quality weld, thanks to the optimal welding parameters chosen by the DSS, is the extension of the end product’s lifetime since low quality welds could lead to premature failures. RoboWeldAR, thus, achieves an increase in the durability of products which affects the circularity of the entire process.
How will your solution be replicated and used in other manufacturing environments?
RoboWeldAR is an intelligent, modular and configurable robotic platform. It requires a relatively small upfront investment making it ideal for small to medium scale enterprises that wish to remain flexible while automating certain processes. Its small footprint and programming free nature lowers the barrier to entry even more. Thanks to its integrated automatic tool changer mechanism, RoboWeldAR can accommodate a wide range of sensors, tools and end-effectors that enable it to perform different tasks according to the needs of each manufacturing environment. Small, targeted modifications to the Augmented Reality application as well as to the Decision Support System can also tackle the unique challenges present in different industries. Currently, RoboWeldAR plans to become a valuable asset in the ship repair domain but can easily be installed in any machine-repair shop that performs welding tasks. In summary, although RoboWeldAR is being developed with a focus on welding, the platform is suitable for almost any material handling application.
What advice would you give to companies wishing to make their manufacturing processes more circular?
To make manufacturing processes more circular, companies should adopt a circular by design approach to product design. This involves using materials that can be easily reused, repaired, or recycled to reduce waste and emissions during production. Closed-loop systems can also be adopted, allowing companies to reuse materials and energy in their production processes. This minimises the need for new resources and reduces waste from one process by using it as a resource in another.
Collaboration with stakeholders in the supply chain, including suppliers and customers, is important for implementing circular solutions. New technologies such as digital platforms and 3D printing can also be embraced to enable better tracking and management of resources and reduce waste.
Employee and customer education is also essential for promoting circular manufacturing. This includes training employees in circular practices and communicating with customers about responsible disposal of products. Finally, companies should measure and track their progress towards circular manufacturing to identify areas for improvement and demonstrate their commitment to sustainability.
To summarise, circular manufacturing involves a redesign of products to reduce waste and emissions, adoption of closed-loop systems, collaboration with stakeholders, embracing new technologies, educating employees and customers, and measuring and tracking progress. By implementing these strategies, companies can contribute to a more sustainable and circular economy.
* * * * *
About the PUMP project
The RoboWeldAR project – Cognitive robotic welding solution for Shipbuilding 2.0 – is implemented by three partners: IKnowHow SA (Greece), Carell SA (Greece), KiNNO Consultants (Greece)
Summary: The main objective of the project is to deliver a robotic welding system which will automate highly custom tasks in agnostic and ever changing environments, such as shipbuilding and repair operations in the shipping industry, by performing high quality and safe welding tasks, while providing technicians with the ability to monitor and easily insert custom welding trajectories