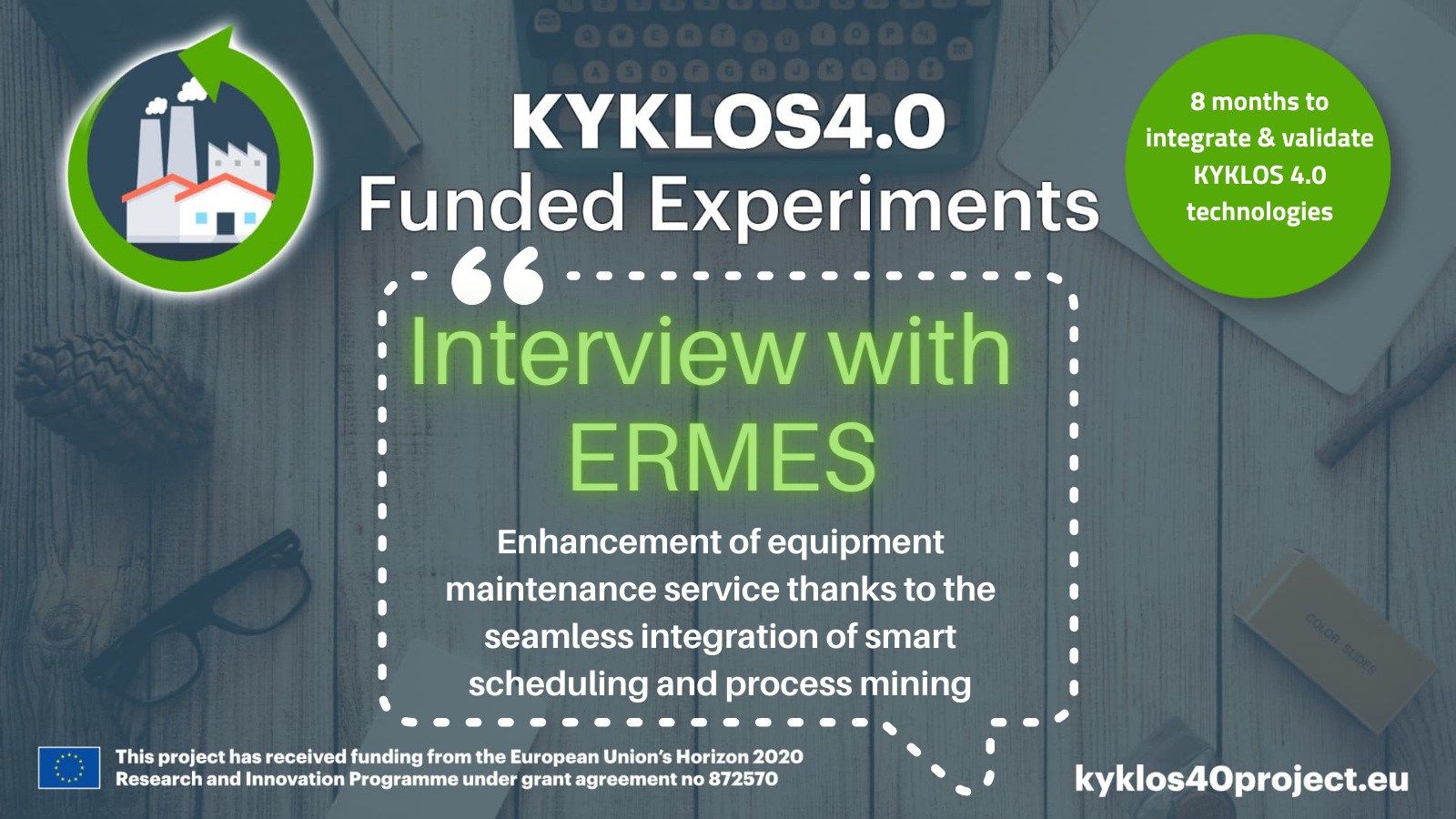
12 May Interview with the ERMES experiment
The KYKLOS4.0 Open Call #2 is funding seventeen experiments that are developing technological solutions of value for the manufacturing domain.
The project will be releasing a series of interviews over the course of the coming weeks with the objective of promoting the work being implemented in these experiments and allowing our readers to understand potential uptake of the solutions being developed by them.
This is the ninth of the seventeen interviews with the experiments funded under the open call. Today, we interview the ERMES experiment.
* * * * *
Explain your project in one sentence.
The ERMES solution aims to enhance and optimise maintenance service of production equipment/machine tools through seamless integration of AI-powered process mining techniques and smart scheduling. The final goal is setting up process paths that require minimal costs, resources and time.
How is KYKLOS4.0 project and the selected services (and components) bringing value to your project?
The overall maintenance service process includes upstream tasks (the higher-level process aspects and actions related to organisations of maintenance service, including logistics and spare management/delivering), and the downstream tasks (edge maintenance activities) that includes strategies and scheduling of maintenance tasks on the machine to repair failures/malfunctioning. Process mining solutions developed by the ERMES partners are primarily focused towards the optimisation of upstream tasks specifically as well as the whole process in general. KYKLOS 4.0 project and selected service (maintenance scheduler) support the experiment in improving the downstream tasks. Some features of the selected service include: automatic trigger of equipment maintenance schedule, work instructions for maintenance activities, database of issues for each equipment when maintenance is performed, automatic spare parts trigger and delivery based on planning, automatic ticketing, etc. Therefore, the expected enhancements will provide a smart maintenance scheduling which is based on optimal allocation of resources, enabled preventive strategies and minimal equipment downtime.
How is your solution contributing to circular manufacturing?
ERMES provides a critical solution which is pivotal to the transition towards a more circular manufacturing. The methodology utilised in the project enables a deep integration and optimisation of the overall maintenance process. This approach will boost process re-use and refurbishment by extending the useful life of equipment, reducing the waste disposed and enabling efficient planning and execution of logistics and also the maintenance related tasks. AI-powered process mining is a challenging endeavor. The method has attracted a significant amount of attention in recent literature. The exploitation of such an approach to achieve optimised maintenance service in the sector of machine tools is innovative. Business process mining is a new academic/research discipline that falls between machine learning and data mining and on the other hand it deals with process modelling and analysis. The resiliency of the entire workflow can be strengthened by the integration of smart maintenance scheduling and process mining applications. Safeguarding maximum efficiency for the entire maintenance service processes comes down to ensuring reliability. As a result, the useful life of equipment is extended, waste is reduced and the circular economy is enabled.
How will your solution be replicated and used in other manufacturing environments?
The ERMES solution incorporates a deep-dive analysis, discovery, monitoring, and enhancement of existing maintenance service processes, and identifying potential efficiencies for the business which they could benefit from. It takes all of the process data generated by a business process and mines it for insight on potential improvement, focusing on finding better and more efficient pathways in operations. The goal is to identify optimal process pathways that lead to minimal cost, time and resources. This enables the business to improve speed and accuracy, allowing teams to focus on doing what they do best in the most efficient way possible. The solutions within ERMES will be developed for machine tools/production equipment sectors but can be replicated in different manufacturing sectors, especially where maintenance services take place, such as manufacturing of automotive, aerospace and energy components, telecommunication sectors etc. In fact, the ERMES tool ingests any event logs file that are generated by the IT system (or manually by operators) within a business process; such log files could be pre-processed just to include the attributes/features required by a maintenance service-related process to enable the ERMES tool to parse it in a proper way.
What advice would you give to companies wishing to make their manufacturing processes more circular?
Basic advice would be the following:
- Properly manage the end-of-life strategy of your product. In case of reuse of equipment, it is really necessary to know its actual status at the end of life in order to make the proper decision needed to extend the life. To do that, it is important to collect data during the equipment operative life that can help in some way decision makers in taking the proper decisions (e.g., about renovation, retrofitting, remanufacturing etc.)
- Design your products for circularity: if you produce a physical product, its design is of paramount importance for closing the loop. For example, you can include design/assembly features that support remanufacturing/retrofitting at the end of life. This may seem pretty straightforward, but it can actually be a complex process, often balancing functionalities that can oppose and cancel each other out.
- Collaborate with all suppliers/stakeholders in your product’s lifecycle. To successfully close the loop for a product requires the cooperation of all the actors who interact with it throughout its lifecycle. Everyone has to contribute in some way towards the implementation of circular concepts and your company has to manage this collaboration.
* * * * *
About the ERMES project
The ERMES project – Enhancement of equipment maintenance seRvice through seemless integration of sMart schEduling and proceSs mining – is implemented by two partners: AXIRO Italia Srl (Italy), UTENSILERIA VALTELLINESE Srl (Italy).
Summary: The main objective of the project is to enhance and optimize Maintenance Service of production equipment/machine tools through seamless integration of AI-powered process mining techniques and smart scheduling.